Three Phase Induction Motor
In the case of 3- phase AC operation three phase induction motor is the most widely motor. As this type of induction motor does not require any starting device so for this reason three phase induction motors are called self-started induction motors.
Three phase induction motor is one of the most popular types of AC motor. The three phase induction motor is a singly excited AC machine that is supplied power from a single ac source.
In three phase induction, the motor stator is directly connected to the AC source and its rotor winding receives energy from the stator by means of induction (i.e transformer action). Due to this reason this motor is called an induction motor.
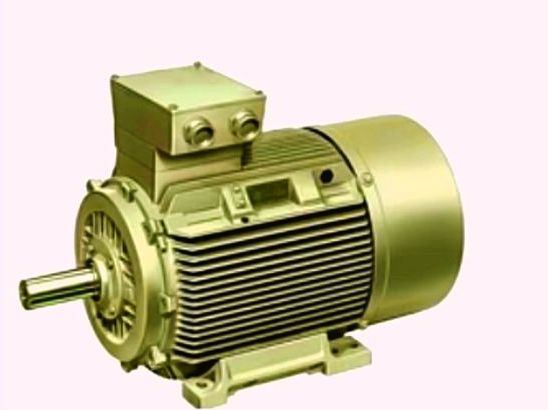
As mmf wave produced by stator and rotor is stationary with respect to each other, Then consequently there is a development of a steady electromagnetic torque is possible at all speed but not at the synchronous speed.
Mmf wave of stator and rotor combine to give the resultant air-gap flux density wave of constant amplitude and rotating at synchronous speed, which means an induction motor cannot run at synchronous speed so its speed is called asynchronous speed and it is called as asynchronous type motor.
Construction of three phase induction motor
Three phase induction motor essentially consists of two major parts :(i) stator and (i) Rotor. The detailed explanation about the stator and the Rotor of a three phase induction motor is discussed below.
Stator
As the name indicates, the stator is the stationary part of the three phase induction motor. The stator is made up of high-grade steel alloy steel laminations to reduce eddy current losses in the machine.
The laminations are slotted on the inner part of the stator and are insulated from each other. A stator frame of cast iron or fabricated steel is also present to support the laminations present.
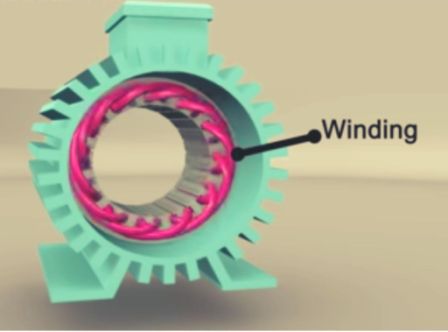
The three phase winding that is present in the stator slots are arranged in such a way that these windings produce a rotating magnetic field when three phase ac supply is given to them. All these windings of the stator are electrically spaced 120 degrees apart.
Here the three phase windings may be connected in star or delta depending upon the requirement. Stator also has an outer frame or yoke on which a terminal box is mounted. From the terminal box, three leads are taken out and from these three leads, three phase supply is connected.
In between the windings, insulation is present which is generally varnish or oxide coated. The figure of the stator with its parts is shown below.
ROTOR
Rotor means the rotating part of 3 phase induction motor. It is also built up of thin laminations of the same material as the stator. The rotor of the 3-phase induction motor consists of a cylindrical laminated core with parallel slots which carry conductors.
The conductors used are bars of copper or aluminum which fits in the slots and these bars are short-circuited by end rings of the same material.
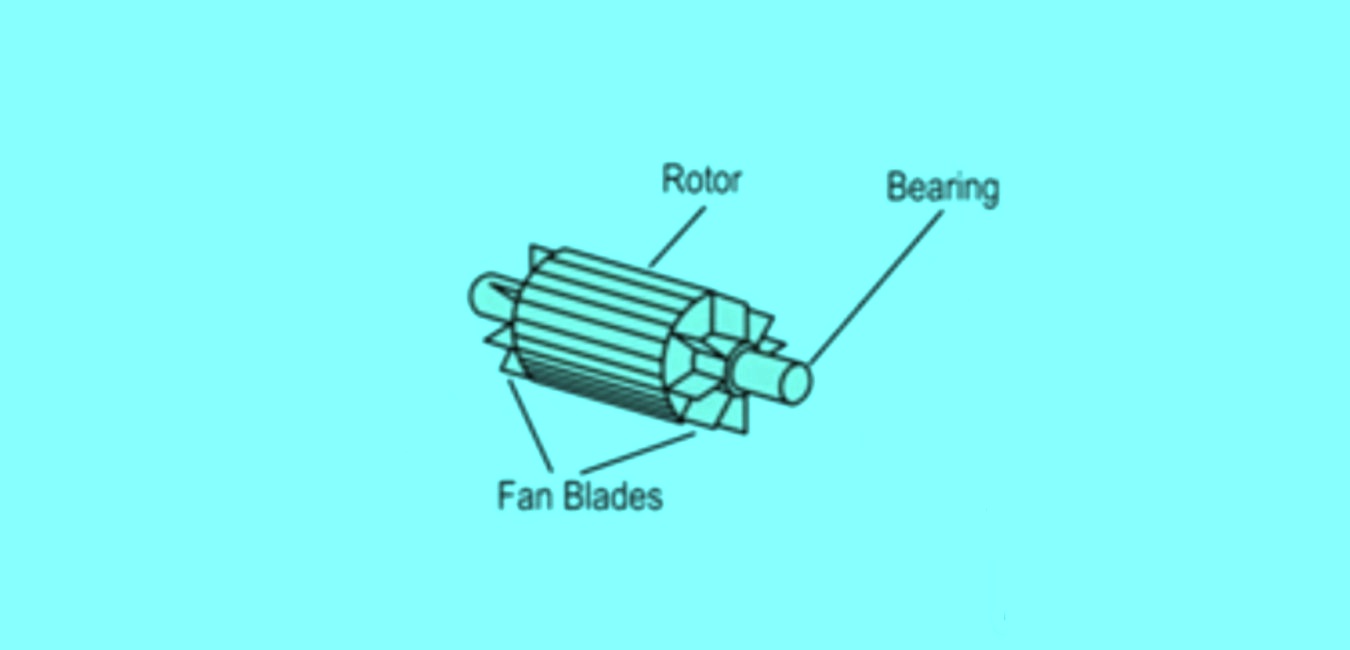
The slots are made a little skewed to the axis of the shaft and are not exactly parallel to the axis of the shaft. These slots are made a little skewed to the axis of the shaft because this type of arrangement reduces magnetic humming noise and can avoid stalling of the motor.
In the case of an induction motor there are two types of rotors.
- Squirrel cage rotor or simply cage rotor.
- Wound rotor or slip ring rotor.
In both the type of rotor slots are not made parallel to the axis of the shaft i.e the rotor slots are a little skewed to get a noise-free and smoother operation of the induction motor.
In addition to the stator and rotor, a fan system is also attached to the rotor shaft. The function of the fan in the motor is to blow out air over the casing to cool it down because the induction motor produces a lot of heat during its operation.
On the outer surface of the motor, fins are present. The fins increase the surface area which allows dissipating the unwanted heat of the 3-phase induction motor.
Before understanding the working of three phase induction motor we have to first understand the concept of the rotating magnetic field. So the concept of rotating magnetic field (RMF) is discussed below.
Rotating Magnetic field (RMF)
When a balanced three phase is given to a three phase winding then a rotating magnetic field (RMF) is produced. The rotating magnetic field is such that its poles do not remain at a fixed position on the stator but it shifts their positions around the stator.
Due to this reason, it is called a rotating field. The magnitude of this rotating is constant and equal to 1.5φm. Here φm is the maximum value due to any of the phases.
Working principle of three phase induction motor
Let us consider apportion of a three phase induction motor as shown in the figure for understanding the working principle of the motor.
When three phase ac supply is given to the three phase stator winding then a rotating magnetic field (RMF) is established which rotates around the stator at synchronous speed.
The rotating magnetic field passes through the air gap and cuts the rotor conductor which as yet stationary. Due to the relative speed between the rotating flux and the stationary rotor conductor, an emf is induced in the rotor conductor by the faraday law of electromagnetic induction.
As the rotor circuit is complete, either short-circuited through the end rings or through an external resistance then a current starts to flow in the rotor conductor due to the induced emf. By using Flemings left-hand rule, the direction of induced current can be found.
The rotor conductor carrying the current is placed in the rotating magnetic field produced by the stator. Then a mechanical force acts on the rotor conductor. Due to the mechanical forces on all the rotor conductors, a torque will act upon the rotor which tends to move the rotor in the same direction as the rotating magnetic field.
The fact that the rotor is prompted to follow the stator field, means the rotor moves in the direction of the stator field can be explained by Lenz law.
Here according to Lenz law, the Direction of the rotor current will be such that it tends to oppose the relative speed between the rotating field and the stationary rotor conductor which is the cause of the production of rotor current.
So as to reduce the relative speed, Rotor starts to run in the same direction as that of the stator field and tries to chase it.
Three phase induction motor has various advantages which made it more useful for most applications. The advantages of three phase induction motor are discussed below.
Advantage of Three-phase induction motor
- 3-phase induction motors are simple and robust in their construction.
- It is less expensive due to its simple construction.
- Less maintenance is required in this type of motor.
- It is a type of self-excited motor.
- The output of the three phase induction motor is 1.5 times the rating of a single phase induction motor of the same size.
Disadvantages of Three phase induction motor
- When the load on the motor increases then the speed of the 3-phase induction motor decreases.
- Torque in the case of three phase induction is lower in comparison to double cage induction motor.
- In comparison to dc motor speed control of the 3-phase induction motor is difficult.